PET plastic cups are typically manufactured using a process called injection molding. Here are the general steps involved in the manufacturing process:
Raw material preparation: The primary raw material used in PET cups is PET resin. The resin is first melted and then fed into an injection molding machine.
Injection molding: The melted resin is injected into a mold cavity using high pressure. The mold is typically made of two halves that are held together by a clamp. The mold is designed to form the shape of the cup.
Cooling: Once the mold is filled with the melted resin, it is cooled to allow the plastic to solidify and take on the shape of the mold.
Ejection: The mold is then opened, and the finished cup is ejected from the mold cavity.
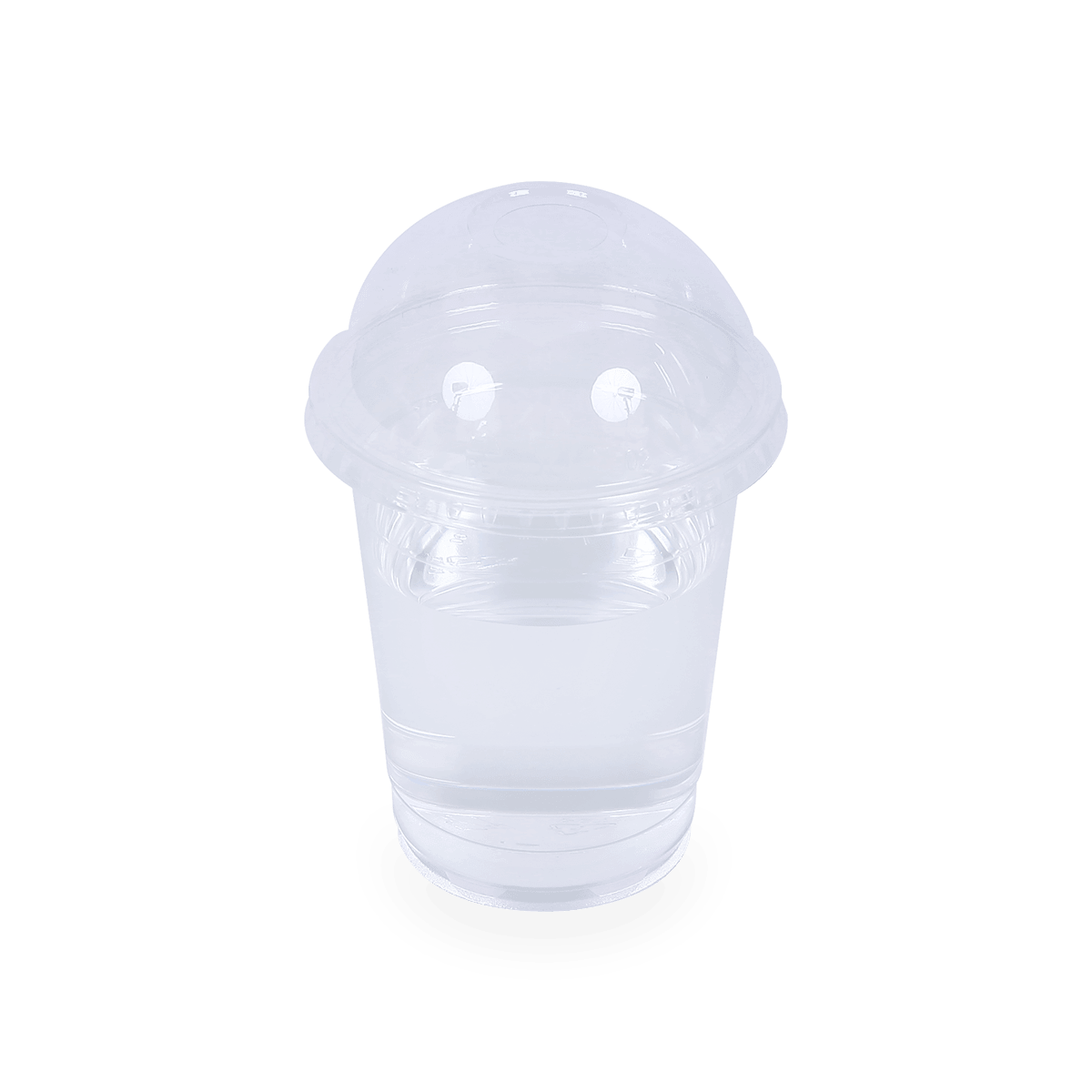
Trimming: After the cup is ejected, any excess material is trimmed away from the edges of the cup.
Quality control: The cups are inspected for quality to ensure that they meet the desired specifications.
Packaging: The cups are then packaged and shipped to customers.
Overall, injection molding is an efficient and cost-effective way to manufacture large quantities of PET plastic cups quickly and consistently.