Here is a simplified overview of the manufacturing process for
CPET trays, which are commonly used:
Material Selection: Manufacturers select the appropriate plastic material for the pallet based on factors like load capacity, environmental conditions, and intended use.
Molding: The selected plastic material is typically processed through injection molding or structural foam molding techniques. Injection molding is more common for rigid plastic pallets, while structural foam molding is used for heavier-duty pallets.
Mold Design: The pallet's design and specifications, including dimensions, deck style, and any additional features like reinforcement ribs, are programmed into molds.
Heating and Melting: Plastic resin pellets are heated until they melt into a liquid state. For structural foam molding, a blowing agent is injected into the melted plastic to create a cellular structure, reducing material usage and weight while maintaining strength.
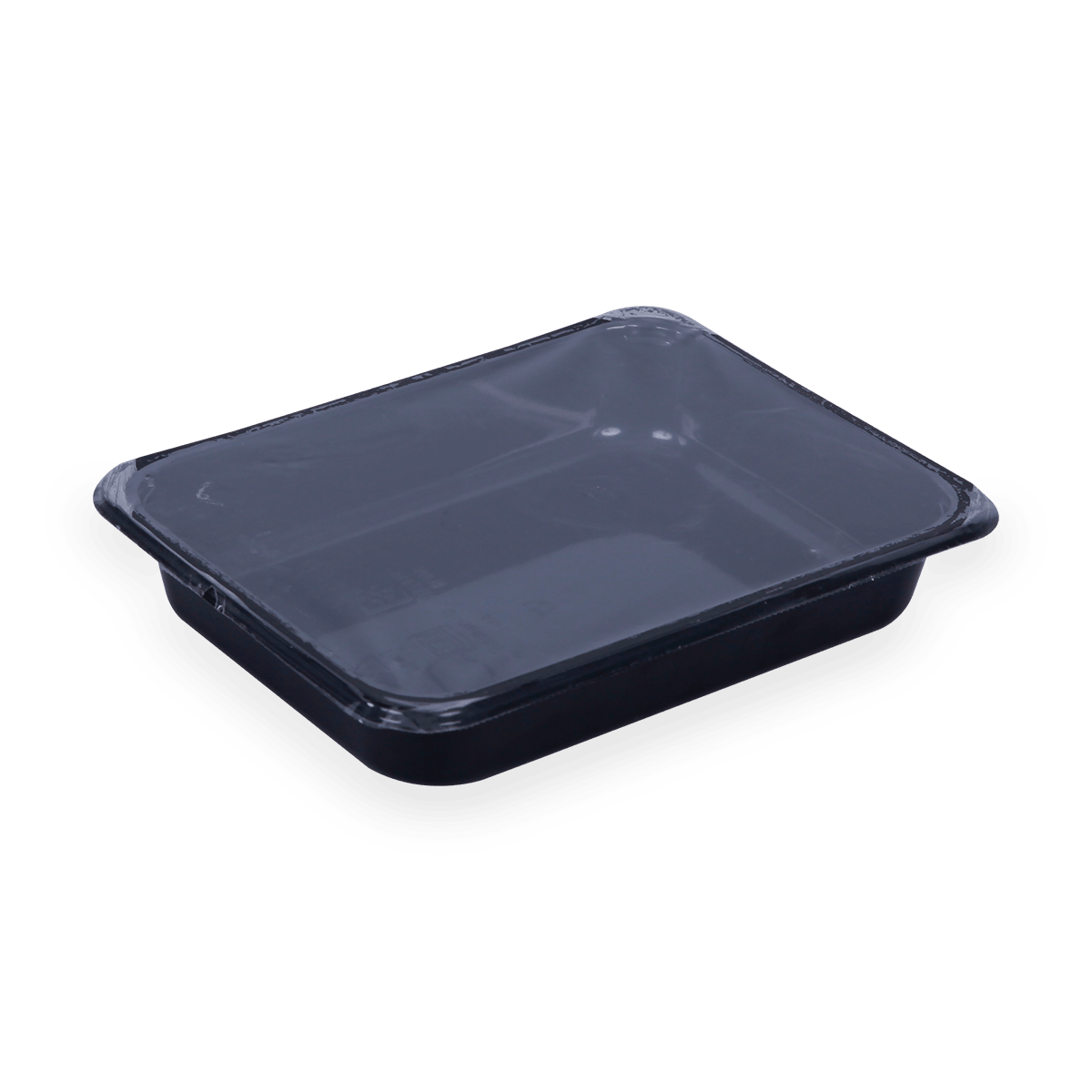
Injection or Compression: The molten plastic is injected into the mold under high pressure. In the case of structural foam molding, a chemical blowing agent expands the plastic inside the mold cavity.
Cooling: The plastic inside the mold is allowed to cool and solidify, taking on the shape of the mold.
Ejection: Once the plastic has cooled and hardened, the mold opens, and the newly formed pallet is ejected.
Trimming and Finishing: Any excess plastic or flash is trimmed from the pallet, and additional finishing processes may be applied, such as adding anti-slip features or labeling.
Quality Control: Pallets undergo quality control checks to ensure they meet the specified standards for strength, size, and other characteristics.
Packaging: The finished pallets are packaged and prepared for distribution.